Методы контроля закаленного слоя крановых колес
На предприятии создана и постоянно совершенствуется собственная система улучшения рабочей поверхности кранового колеса: мы научились производить снижение градиента твёрдости в глубину колеса в более строгом диапазоне, чем регламентирует п. 2.4 ГОСТ 28648-90.
Участок термообработки обеспечивает шахтная печь, позволяющая задавать и контролировать большой диапазон различных параметров нагрева: интенсивность, время заданной температуры, постоянство нагрева с точностью ±1ºС. Именно в печь помещается колесо сразу после первичной механической обработки.
Далее колесо попадает в установку, где происходит охлаждение и закалка рабочей поверхности (обод / катание, реборды). Нерабочая поверхность колеса (ступица, зеркало) охлаждению не подвергаются.
Охлаждение рабочей поверхности происходит в заданной, контролируемой динамике: колесо вращается в замкнутом кольце спрейера (душирующей установке), охлаждающий реагент подаётся под определённым давлением. Температура охлаждающей среды при этом контролируется.
Стабильным результатом данного этапа является улучшенная рабочая поверхность колеса с глубиной закалки 320...390 НВ в зависимости от типоразмера колеса, с твёрдостью и упругостью нерабочих зон.
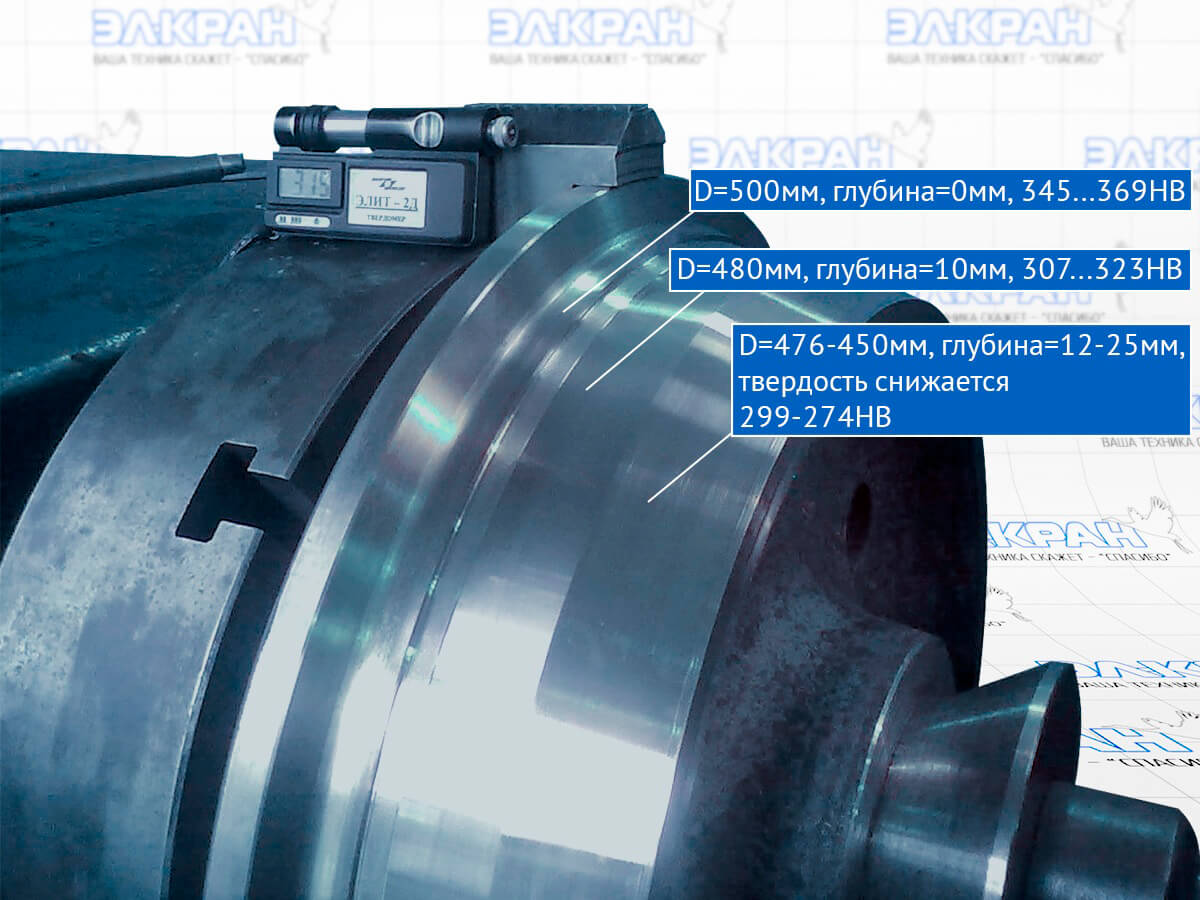
Плановая периодичность проверки глубины термообработки: при годовом выпуске колес от 40 до 200 шт. - не реже одного раза в 5 лет и при годовом выпуске свыше 200 шт. - не реже одного раза в 3 года, но не менее 1-го колеса из каждой 1000 изготовленных (П.3 ГОСТ 28648-90. Колеса Крановые. Технические условия).